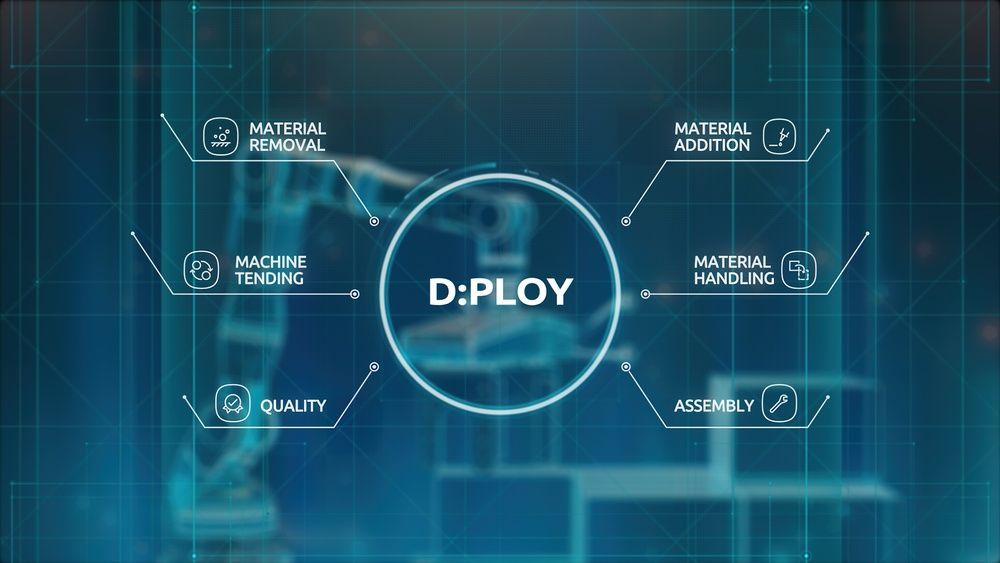
D:PLOY - The next big leap in automation
D:PLOY - The next big leap in automation
OnRobot, the One Stop Shop for collaborative robot applications, provides a wide assortment of tools and solutions for collaborative applications including electric, vacuum and magnetic grippers, Gecko gripping technology, force/torque sensors, vision systems, screwdrivers, sander kits and tool changers. Headquartered in Odense, Denmark, OnRobot also has sales offices in Europe, North America and Asia, and a large R&D center in Budapest. OnRobot is committed to removing barriers to automation adoption by bringing to the market solutions and technologies, that are affordable, accessible and create substantial value for companies of all sizes. D:PLOY is the industry’s first automated platform for building, running, monitoring, and re-deploying collaborative applications. It automates the process of getting a robotic application up and running, allowing deployment directly on the manufacturing floor, with zero programming and simulations. With D:PLOY, complete applications can be deployed in just a few hours.
Our partner said
Overview
D:PLOY by OnRobot is the next big breakthrough in industrial automation that democratizes robotic technology. D:PLOY simplifies robotic automation so that you can enter the field with ease and flexibility. When compared to previous traditional solutions, D:PLOY offers substantial deployment and re-deployment time reductions of up to 90%, allowing you to enjoy the advantages of automation finally. D:PLOY enables you to adopt automated changes in your production more quickly and affordably while maintaining control over continuing costs by speeding up deployment and re-deployment times.
Nearly all of the installed hardware is automatically found by D:PLOY. You no longer have to spend much time installing or programming the interface to operate tools and other cell components, or setting up the robot. Users of the workspace definition can set workspace barriers and cell borders using the user-friendly graphical interface. Depending on the defined barriers, D:PLOY builds a collision-free path automatically. Palletizing, packaging, machine tending, and transferring are four basic robotic applications that may be set up at the programming interface by entering workpiece qualities, pick position, and other application inputs using a straightforward step-by-step flow. The program logic, signal exchanges, event handling, and path planning for the complete application are generated and optimized automatically by D:PLOY. You can run your application with a single click. Get real-time monitoring insights into performance metrics with minimal configuration to increase productivity and reduce downtime.
Challenges
To create a user-friendly workspace definition, we had to accomplish an interactive 3D model simulation based on the user inputs (multiple separate inputs and user-friendly 3D model transformation with both cursor and touches) as well as optimizing the rendered output to achieve the least resource-intensive task in a proper way.
The entire solution includes different programming layers in which the integration with the manipulator arms, the tools (grippers) placed on the robots, devices (sensors, digital I/O-s, CNC machine) and Cloud had to be ensured.
To program the applications, it is necessary to enter exact size data that has been calibrated for each robot and gripper, but based on actual use cases, the system must be able to make changes on the fly, which requires complex business and technical planning.
Since the applications were executed on actual robots, there were few opportunities for remote integration and testing of the product, thus we improved and tested the solution for the actual robots in person with each iteration.
The D:PLOY web application design had to be responsive to achieve the best result in different screen sizes and hardware and the web application solution had to support different use cases for tablets and desktop.
SnapSoft's Contribution to the Solution
SnapSoft provided three full development teams (2 teams specialised in Web applications and 1 team on AWS Cloud) for the project with their own Scrum Masters with a total of 18 engineers. Later, the client added its developers to the teams and delivered the final solution together. The first development phase took 14 months until the first release, with four robotic applications - Palletizing, Transferring, CNC Machine Tending, and Packaging.
Web application:
SnapSoft provided the D:PLOY web application, which included frontend, backend and integration tasks. The SnapSoft team worked closely with the client's Product and UX teams to clarify business needs. It organised and managed the teams and constantly reported on their progress, and dealt with any problems immediately. Our senior developers participated in the regular architectural planning to reach the most easily maintainable, flexible, and scalable architecture. The completed application was continuously tested by the SnapSoft engineers online and in person during the iterative development.
Main parts:
- Configuration cards for all supported robots, tools and devices to assemble the robot cell
- Real-time status display and monitoring of different robot types, tools and devices
- Intuitive 3D graphical interface to set obstacles and cell boundaries
- Step-by-step application flows to enter workpiece attributes, pick a position and other application inputs, with several automated solutions like pattern editors, signal exchanges, event handling and path planning.
Cloud:
The SnapSoft Cloud team migrated to the AWS cloud and modernised the on-premise WebLytics functionality as well as built a scalable, high-available, and fault-tolerant AWS infrastructure solution using a wide range of AWS services. The microservice-based AWS infrastructure manages critical parts of the solution and provides continuous backup. The new cloud-based Weblytics solution can collect, analyse and visualise data of industrial robots smoothly.